2020 Construction Trends Forecast
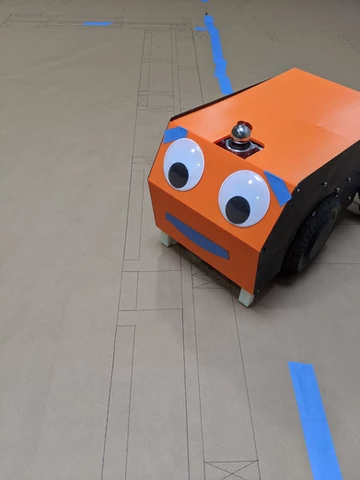
At Dusty Robotics, we spend a lot of time talking to professionals in the construction industry about how the industry is evolving to increase productivity and cope with a widespread skilled labor shortage. Almost everyone believes the labor shortage is here to stay, and will only worsen over time as skilled workers retire and millennials are reluctant to take their place. This labor shortage puts the spotlight on construction robotics in 2020 to close some of this gap and enable construction firms to keep pace with increasing demand despite a shrinking workforce.
However, a number of factors beyond the labor shortage are also coming together in 2020 that are pointing the way towards increased automation on construction sites. Here I’ll summarize the top three trends we’re seeing across the industry.
One: Growing adoption of BIM. While countries such as Australia and the UK are leading the way in terms of BIM adoption, the US is making strides towards using BIM, particularly on large commercial projects. BIM modeling allows design teams to hash out all the details of a building’s design before building starts, reducing surprises and delays during construction. More and more firms are “frontloading” this BIM design and coordination work, yielding a fully coordinated model that is handed off to the field.
For those GC’s and subs who haven’t yet boarded the BIM train, a cohort of service providers is emerging that can perform this BIM design and coordination work on their behalf. These service providers are building businesses that enable mainstream GC’s and subs to remain competitive in the new BIM world. Adopting robotic layout automation enables these service providers to expand their offerings and provide a complete “BIM to field” solution for their customers.
Increased BIM fidelity is also a necessary precondition for robotic solutions because it provides the roadmap or “work instructions” for a robot to successfully perform work on a job site. Whereas human crews could be set loose with just a paper sketch and some rough guidelines (although not recommended), robotic automation requires more precise specification of exactly what is to be built where. This increased design certainty is good for all, not just robots -- the less uncertainty there is about what happens in the field, the less risk is incurred for all trades.
Two: Increased offsite manufacturing. The construction industry is shifting production off the jobsite into factories, making the building process more like manufacturing. By using factory automation to assist in the production of building components, companies are reducing the amount of expensive, scarce labor required to do onsite construction work.
Despite some high-profile startups making shipping-container-sized Lego building blocks, the sweet spot for modular construction seems to be the use of prefabricated wall panels which can be delivered to the site and dropped in place. Robotic assembly is already widely used to manufacture pre-assembled wall panels or roof trusses. Many GC’s we’ve spoken with have explored this technology and are moving it into production, sometimes through investments in subsidiary companies that produce these prefabricated components.
One of the risks of prefab wall panels, however, is that they must be placed very precisely on the deck in order for the pieces to fit together properly. Robotic layout automation, such as provided by Dusty’s FieldPrinter, ensures that the BIM model is transferred precisely to the deck, ensuring that prefab components fit without any waste.
Three: Increasing vertical integration. Traditionally, general contractors have insulated themselves from the risk of construction by subcontracting out all of the work, retaining only a thin profit margin based on managing the work to schedule. The average GC has a profit margin of only 2-3% across the industry.
When much of that risk was due to errors made during construction (e.g. by fallible humans), that model made sense. However, a quest for higher profit margins has been pushing GC’s to take on more risk -- while also mitigating that risk through better coordination, communication, and automation.
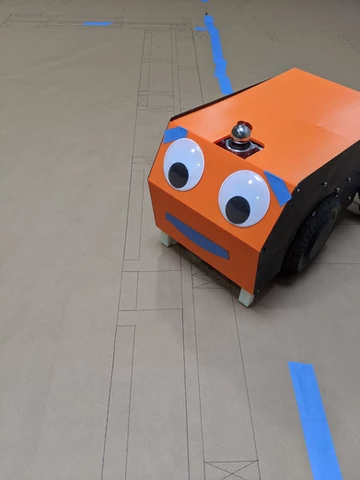
As GC’s are bringing more of the trades in-house, and self-performing building tasks, they are hungry to adopt productivity-enhancing automation. The most advanced vertically integrated GC’s are reimagining traditional workflows to eliminate manual steps and deliver product faster and more cost-effectively than their competition.
Is 2020 the year that you’ll deploy robots on your construction site? Schedule a consultation with us to see how Dusty can help position your business for success in this new decade.