How Dusty Robotics Went Remote
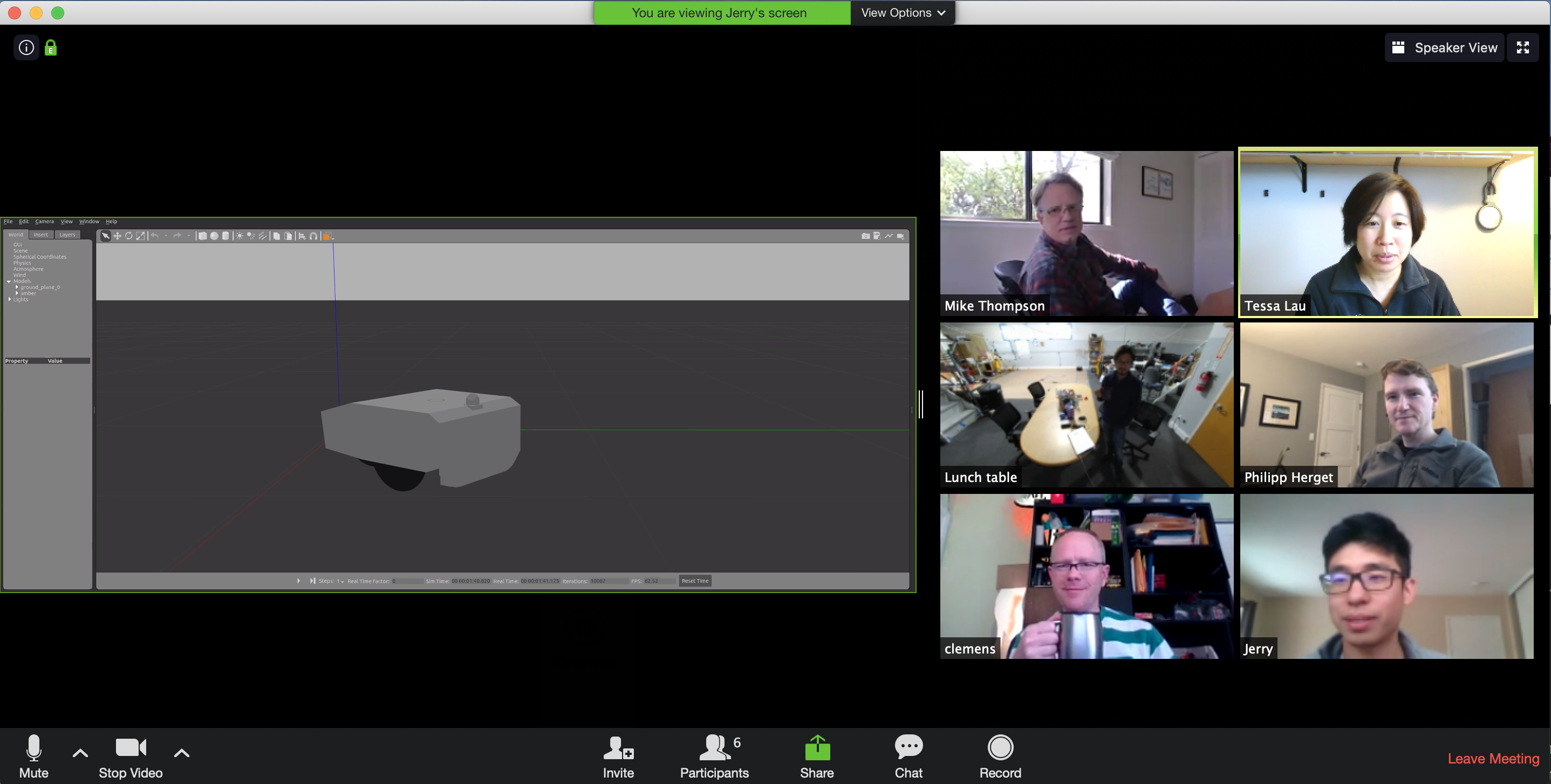
What happens to a robotics company when a shelter-in-place policy goes into effect? We keep building robots, of course! Today we bring you a blog post by our senior software engineer, Clemens Drews:
<Clemens>
When thinking about working from home, robotics always seemed like one of the few areas in high tech where that would be very hard to do. Then comes COVID-19 and here we are coping with the challenge of social distancing while working on robotic hardware that is hard to work on from home.
In early March, it became clear that the COVID-19 virus spread would have an impact on how we work. We decided as a company that it would be necessary for us to figure out how we could implement social distancing while making progress towards our business goals. Some of us immediately started working from home, while the rest of us got everything ready to allow all of us to work in a mode where not more than one of us is at the same place at the same time.
Now if you work in a typical SaaS type of place, your main concern will be bringing your laptop home and converting all your in person meetings to video conferences. But if instead you’re dealing with a robotic system that is expensive and - because it is a prototype - available in very limited quantities, it becomes a little more interesting to get the engineering team to work remotely. Add to that the fact that construction layout is done in large areas usually not found in your typical Bay Area two bedroom apartment. This meant testing the full system at home was all but impossible. We would have to continue operating and testing our system in its usual development environment at the office.
Fortunately most of our digital assets and collaboration tools are already in the cloud, accessible from virtually anywhere: Slack for instant messaging, Github for code and builds, Google Cloud for secure storage and software distribution. We supplemented Google Hangouts with Zoom meetings which the team liked a lot better for e-meetings with more than two people.
To make remote robot work possible, and only have a crowd-of-one at any point in time in the same place, we came up with this:
- One person from the engineering team is in our physical office, rotating weekly. This person - besides doing their normal work - is the robot nanny. Charge, turn on and off the robot and, on occasion, reset the system. They become the hands for the rest of the engineering team.
- The rest of the team connects to the office via virtual private network (VPN) and can control the robots remotely.
- An almost-always-on Zoom e-meeting helps us coordinate and not lose the ability to spontaneously meet and problem solve. Having our peers within shouting distance also gives everyone a sense of normalcy.
- The addition of a remote controllable pan/tilt/zoom camera allows us to monitor the robots and their movements. It even helps us assess our layout print quality from anywhere where we have access to our VPN.
This together with a focus on improving our simulation and test capabilities make it possible for us to maintain our current development speed until the situation allows for us to sit in one location together again, which everyone on the team is looking forward to.
On Friday this week we’ll face the true test: conducting our first remote weekly print challenge. Wish us luck!
</Clemens>
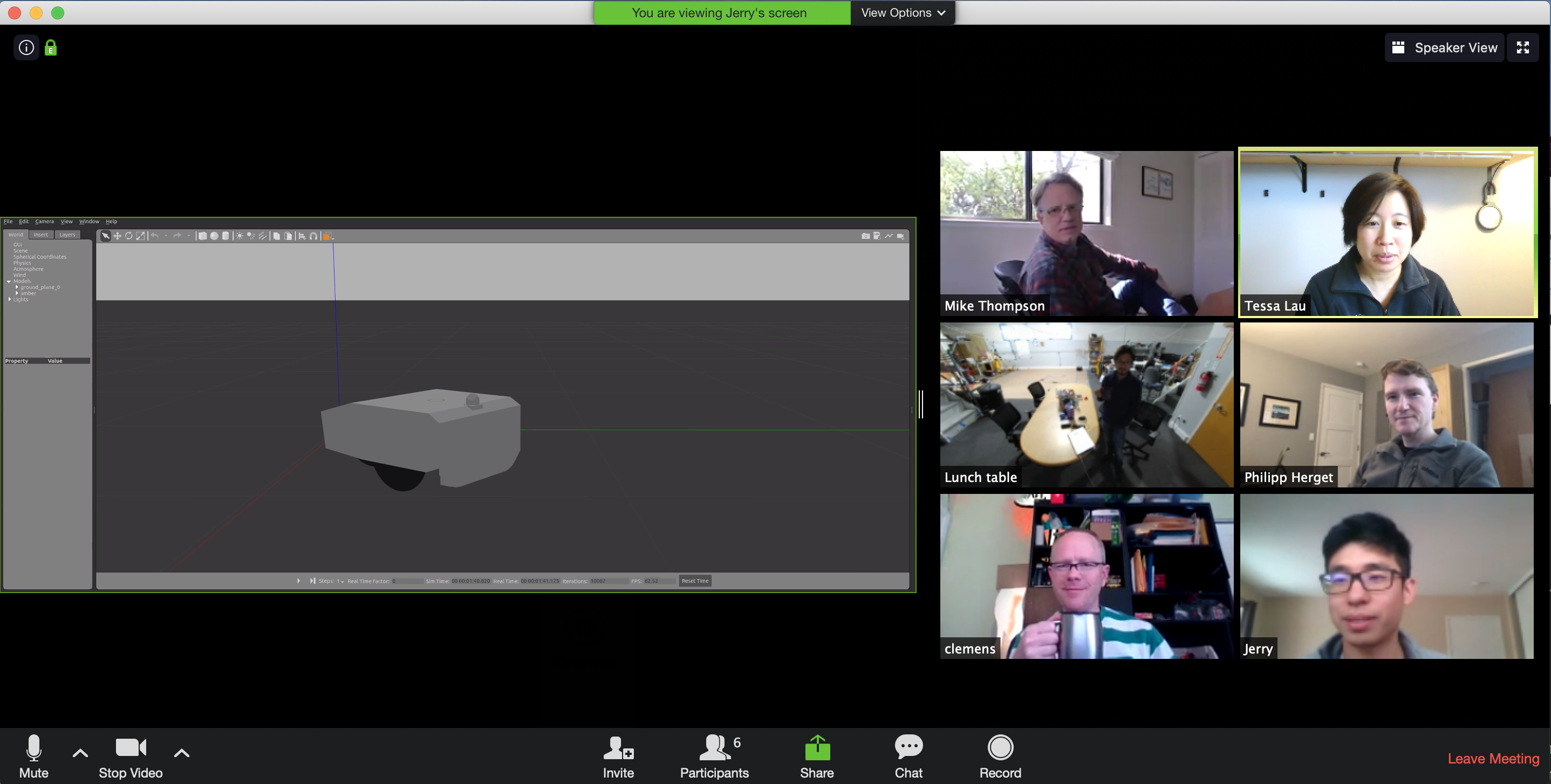