Dale Construction Halves Layout Schedule with Dusty Robotics
Since 1959, Dale Construction—a precision-quality subcontractor—has been framing projects throughout the Philadelphia area. The company has established itself as a regional leader by deploying its team across a variety of projects.
Always looking to improve, the company identified traditional layout as a source of risk to their projects. As Scott Yohe, Dale’s VP of Construction, explained, “Layout is the way we communicate between our company and architects—and everybody else. It takes the plans and gives that information to the workers.”
In other words, it’s a critical (read: high-risk) step of Dale’s process, and one that was ripe for leveraging tech.
The Risks of Manual Layout
The team at Dale Construction identified a few ways manual layout contributed to their risk exposure:
- It’s labor-intensive and requires strenuous, focused work from highly skilled team members—placing their best people at risk of injury and taking them away from other productive work.
- The tools used to perform manual layout have accuracy issues—leading to rework and waste.
- Any shortcomings in a worker’s skill, organization, or bandwidth can compromise layout integrity—again leading to construction defects, errors, and omissions.
As Yohe explained, “With measuring tape, the end starts to move—even an eighth of an inch makes your layout change. When we use chalk to snap a nice long line, that can have a bow to it. And then there’s the possibility of human error. Even the best team members have a different style. Different crews might have to go back and ask, ‘What did you mean here?’”
All of these problems could have been compounded when Dale was tapped to build the four-story Schreiber School of Veterinary Medicine at Rowan University. The project required a short turnaround to accommodate incoming students, meaning Dale needed to get layout completed even faster than normal.
The Dale Construction team saw the opportunity to leverage new technology to deliver an automated layout.
Automated Layout Delivers Gains for Dale Construction
Specifically, Dale looked to the Dusty FieldPrint Platform to meet project demands—and it delivered.
#1: Fast, Accurate Layouts
“Layout was accelerated,” Anthony Deromedi, the Dale Foreman on the project who operated the Dusty FieldPrinter said. “It would have taken me double the time to do that floor by myself with the tape.”
Yohe elaborated further, saying, “We reduced virtually all of our exposure to fatigue injury. We’re not getting up and down at all to snap chalk lines. We found this automated layout was about 50% faster with one operator than manual layout with two people—and that included the time that we trained on it.”
All told, the Dale team saw notable benefits in automating layouts for the veterinary school:
- 75% reduction in layout labor hours
- 95% reduction in strenuous, labor-intensive layout tasks
- 100% accuracy by removing chalk lines and pencils
Plus, Deromedi said, “Dusty was very, very comfortable to use. In fact, I think it’s a little bit easier than the [previously used] digital layout tool. Even adding in alternate control points and all the other nuances with the iPad didn’t take me very long to learn.”
#2: Maximization of Human Talent
The Dusty FieldPrinter can operate with supervision from a single person. “Getting the robot out of the case is pretty much the last time we’re going to be on our hands and knees for the rest of the layout,” Yohe added.
Deploying new tech develops the worker’s leading-edge competencies, too. On learning to use Dusty, Deromedi said, “It definitely makes me more valuable, as a productive member of Dale and as a carpentry union member. If you're on the forefront of technology that's successful like this, you're going to be invaluable to multiple clients and their customers.”
#3: Elimination of Defects
The FieldPrint Platform eliminates the construction defects that result when a manual layout process fails to translate the model perfectly to the jobsite floor. That’s because the FieldPrinter is BIM-connected—taking information directly from the model and printing it with 1/16” accuracy on the jobsite floor.
But it’s not just accurate layout that eliminates defects—it’s the inclusion of more information in the layout. The Dale team used Dusty to add detail to the layout to inform workers and reduce risk of things getting built incorrectly. “We’re able to get a lot more information into the layout with Dusty. For example, you’re able to add writing,” Yohe said. Deromedi elaborates: “We can note double drywall layer walls, door swings, door numbers, or what order to do things in. Dusty helps me give the guys a layout they can really understand.” The FieldPrinter can even print QR codes. Dusty helps Dale get information to field teams so they can work accurately and quickly.
#4: Improved Workflows
Automating the layout delivered efficiency gains. The Dusty FieldPrinter lays out 10,000 to 15,000 square feet in a single day, depending on the project type and density. This supports on-time project delivery.
“Dusty isn’t just assisting us,” Yohe said. “It’s actually doing the work alongside our team.”
Dale used this approach to better inform installers, streamlining their workflows, too.
“We added more information to the layout than ever before, reducing the need to constantly refer to the drawings for additional direction. Our team can look at the additional information and know what they need to do.”
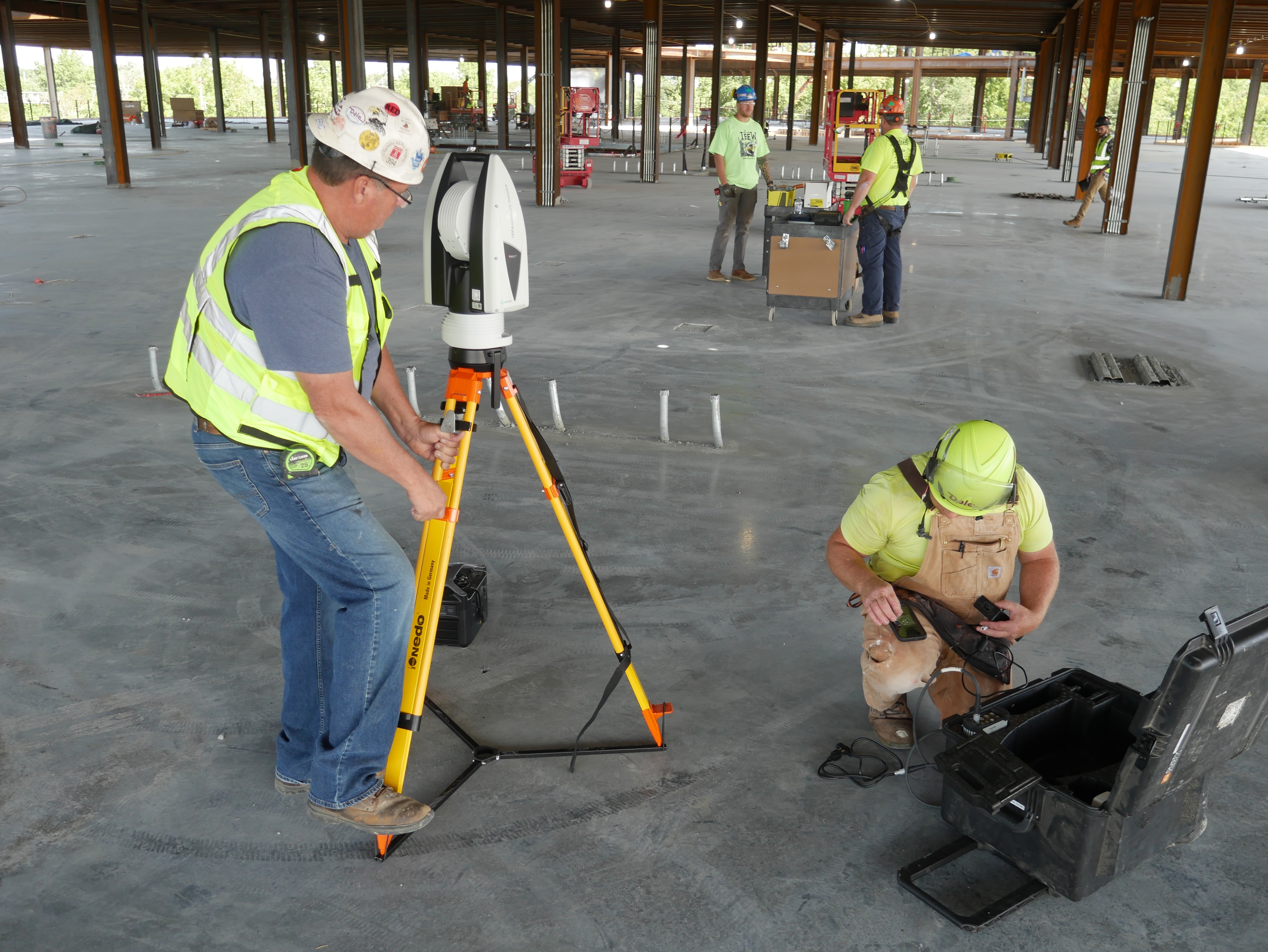
#5: Better Stakeholder Alignment
“Through the Dusty Portal, we’re able to load in what we want to lay out, and it gives us data we need to estimate the time to do the layout. And then, as we’re doing it, it tells us in real time everything that’s going on,” Yohe said.
“There’s no more making a phone call to say, ‘Where are you at? How are you doing?’ You can go on the website and it literally shows the areas that we’ve printed.”
Clarity into project progress is a definite value-add for GCs and owners. And by eliminating the need to manually deliver updates, the Dusty Platform lightened the load for Dale, too.
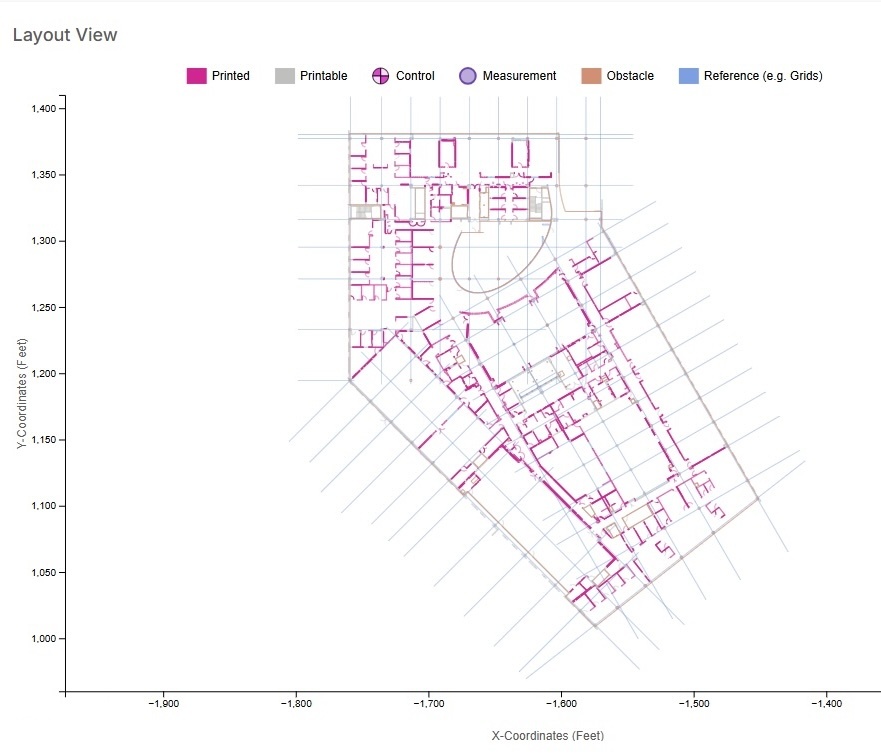
Planning for the Future at Dale Construction
Dale Construction plans to continue leveraging the advantages of automated layout in their future work. They’ll be using Dusty for framing layout at the Children’s Hospital of Philadelphia (CHOP), a major project led by LFDPR, a joint venture of two major GCs, LF Driscoll and DPR. In fact, it’s actually thanks to the LF Driscoll team and early discussions around the CHOP project that Dale first became aware of Dusty’s solution.
Further, on an upcoming project with Skanska, Dale Construction is planning to implement a multi-trade automated layout process. They’ll be building on the success of projects like the Rowan Vet School to further improve their processes. As Yohe explained, “At Dale Construction, we’re focused squarely on the future. When all is said and done, we have all of this data on what we’ve done and how much we’ve been able to achieve.”
That kind of partnership hasn’t gone unnoticed or unappreciated by GCs. “The next iteration in value is multi-trade layout,” said Paul Guelich, Senior Project Manager at Skanska. “I wholeheartedly believe that, from a Lean Construction standpoint, that’s where we maximize this new approach.”
As a way to speed layouts while reducing the risk associated with them, automated layout helps framers like Dale Construction realize wins.
Deromedi summed it all up succinctly. “Dusty is going to be—and already is—the future of layout. I can't see us ever reverting back to traditional manual layout on larger scale projects.”
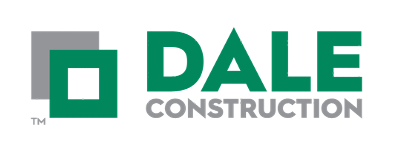
Interested in learning more about the
Dusty FieldPrinter?
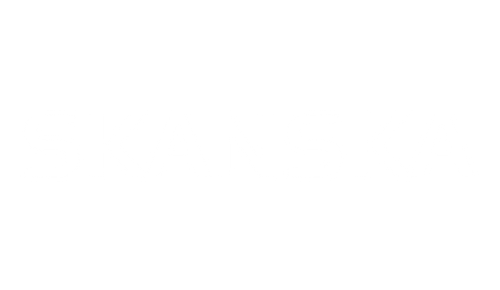
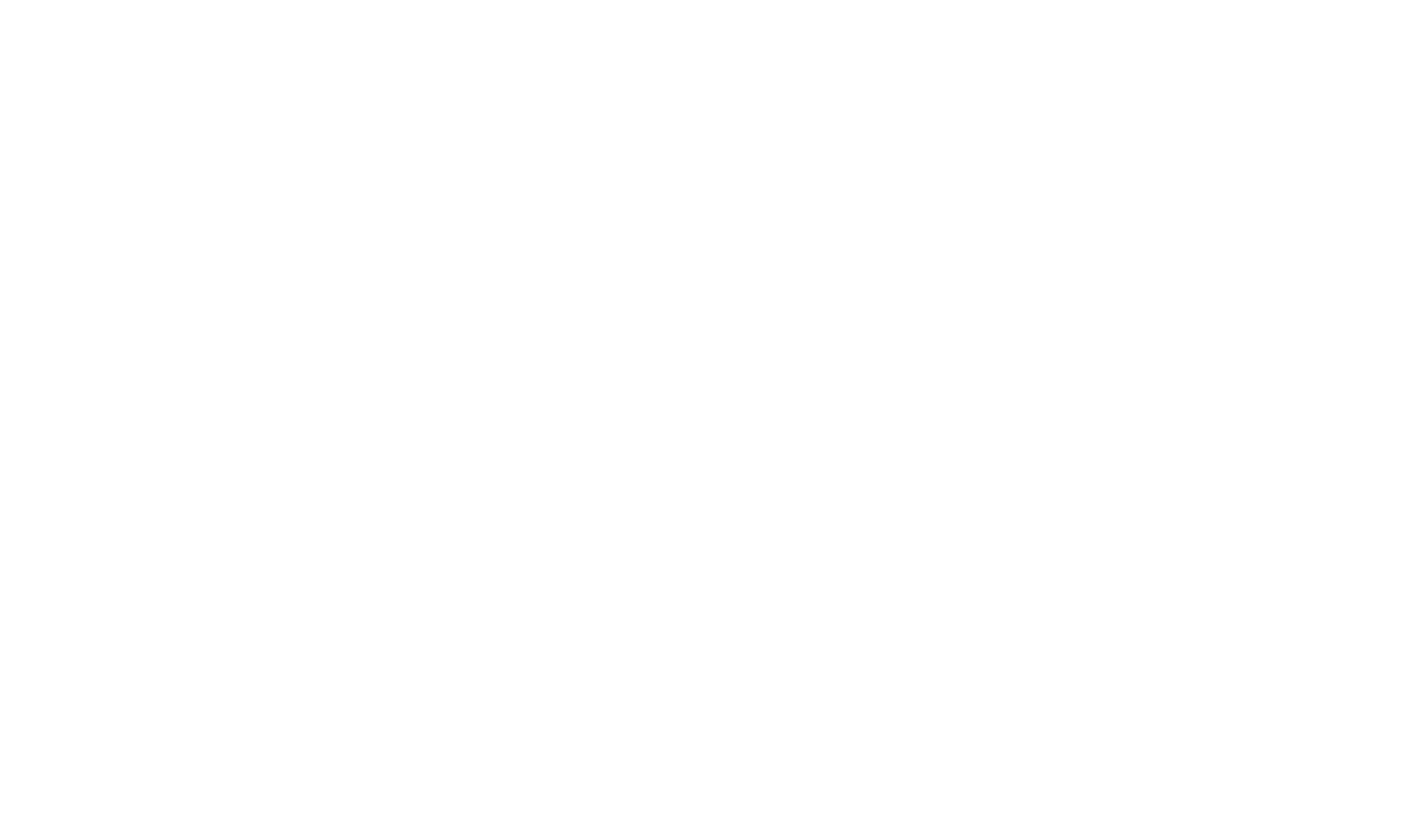
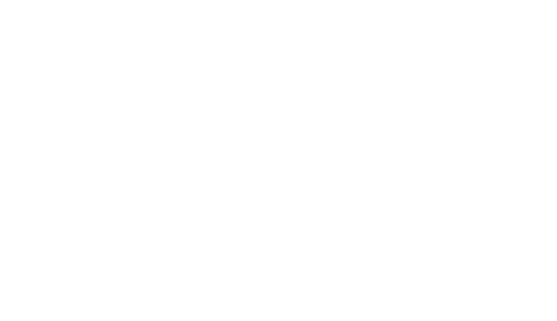
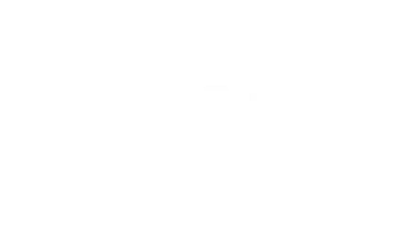
.png)
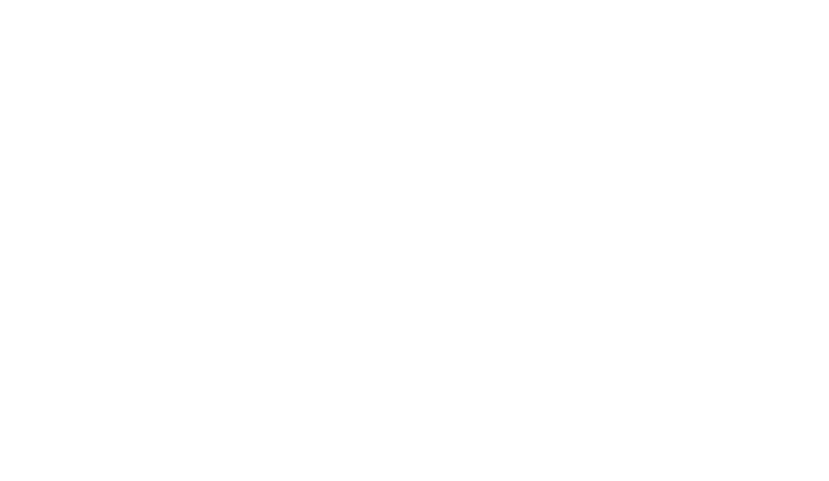