Essential Construction KPIs to Measure and Track
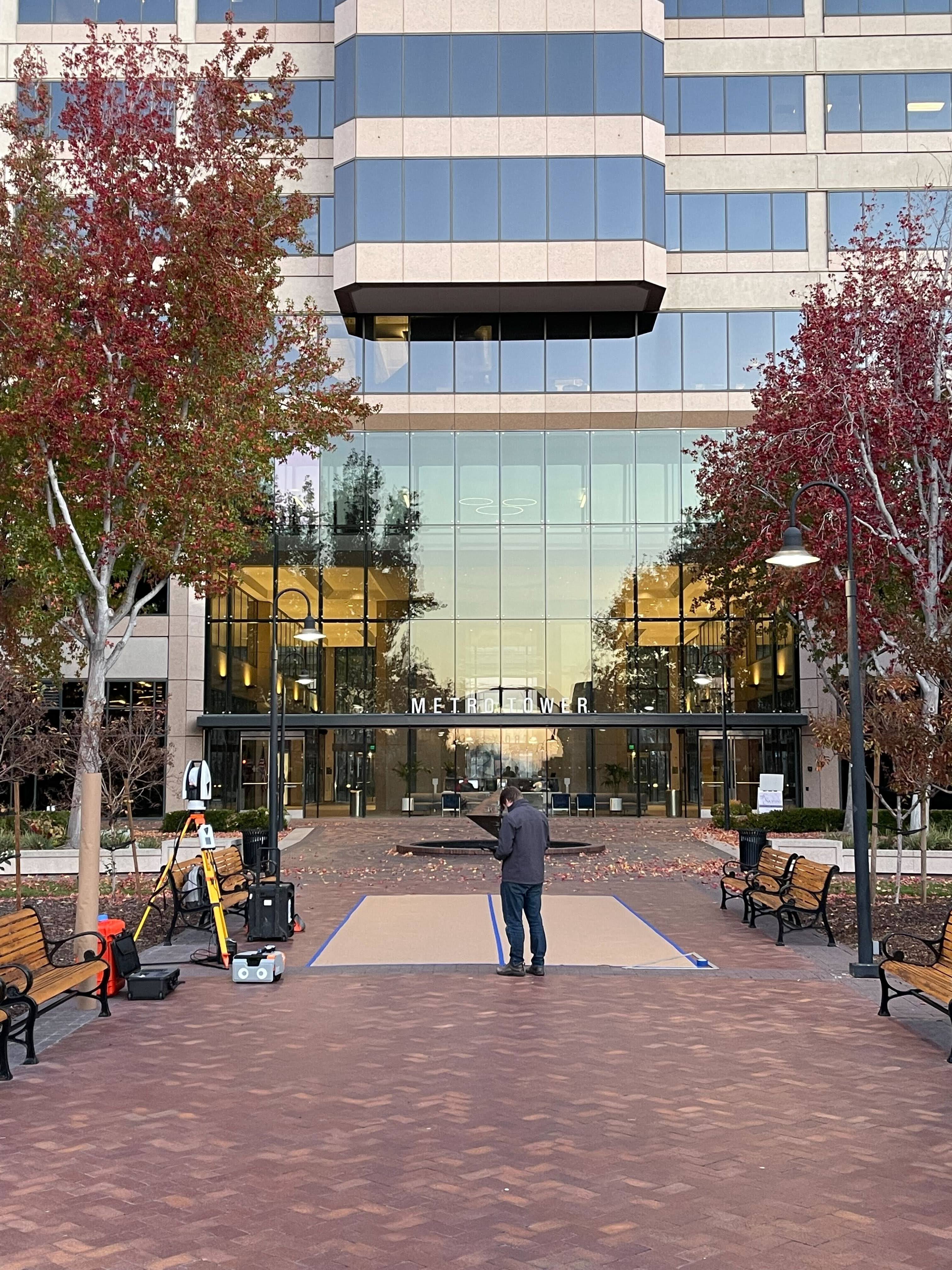
Even the most minor missteps in construction can result in costly, catastrophic failures. Overseeing each aspect of the process is vital, but without systematic tracking, key details may slip through the cracks, risking safety and capital.
Measuring and tracking success ensures projects adhere to standards, budgets, and timelines. Through real-time monitoring and metrics, construction project managers can identify issues and rectify them promptly.
In this article, we’ll explore some of the key performance indicators (KPIs) and strategies employed in successful construction management. Keep reading to learn how to prevent disasters and deliver projects that stand tall and proud.
What are Construction KPIs?
Key performance indicators (KPIs) are a set of quantifiable measurements used to gauge and assess performance. They serve as benchmarks that help businesses and teams evaluate their success at reaching targets and are thus invaluable for continuous improvement.
Construction project KPIs focus on a particular set of metrics throughout the construction project lifecycle. They help stakeholders, from site managers to investors, understand how well a project performs based on predefined targets and industry benchmarks.
These construction KPIs might include cost management, time or schedule adherence, safety performance, work quality, and client satisfaction. For example, one project may focus on a KPI related to the percentage of tasks completed on time or the number of safety incidents reported within a specific period.
Construction firms can look at these indicators to effectively measure their efficiency, productivity, and overall success. KPIs provide a tangible means of assessing the health of projects and identifying areas that may need more attention or a change in strategy.
What are the Different Types of Construction KPIs?
Construction KPIs can be grouped into four primary categories: financial, operational, safety, and quality.
- Financial KPIs: These metrics provide insight into a project's financial health. They help stakeholders determine whether or not the project is on budget and if it's yielding the expected financial returns. Examples include return on investment (ROI), cost variance (CV), and cost performance index (CPI).
- Operational KPIs: Operational KPIs measure the efficiency and effectiveness of different construction processes. They track how well resources are utilized, how closely the project adheres to its timeline, and general operational efficiencies.
- Safety KPIs: Construction sites can be hazardous, making safety KPIs critical. They measure the frequency of accidents and other indicators of a safe working environment.
- Quality KPIs: Making sure the final product meets desired standards is paramount. Quality KPIs evaluate the standard of work, customer satisfaction, and compliance with industry standards.
Financial KPIs
Financial KPIs measure the financial performance of construction projects. They are critical to ensuring that projects stay on track and are financially viable. By monitoring these KPIs, companies can quickly identify potential financial issues and prevent them from spiraling out of control.
Monitoring financial KPIs helps firms optimize resource use and avoid overspending. Given the nature of construction projects, promoting regular cash flow is vital. Some KPIs offer insights into how quickly a company can collect its receivables and manage its billing.
Here are the most essential financial KPIs in construction:
- Cost variance (CV)
- Return on investment (ROI)
- Gross profit margin
- Cash flow forecast accuracy
- Net present value (NPV)
- Overhead costs
Operational KPIs
Operational KPIs are used to gauge the efficiency, productivity, and success of ongoing construction projects. They’re essentially benchmarks that help stakeholders evaluate how well a project adheres to its established goals, timelines, and budget.
For instance, some KPIs measure progress against the project schedule. This is key to determining how well the project is moving along and what, if anything, should be rearranged to avoid delays and speed things up.
Tracking operational KPIs is also helpful for maintaining the quality of work and upholding critical standards. They play an equally important role in resource management, promoting the optimal use of manpower and materials ultimately saving money. With an industry-wide labor shortage and material shortages, keeping track of resource utilization can also help construction managers identify which aspects of a project need to be more closely managed moving forward.
Common operational KPIs include:
- Construction progress index (CPI)
- Resource utilization rate
- Construction site efficiency
- Change order processing time
- Percentage of labor downtime
One of the most innovative ways to improve operational KPIs involves using automated multi-trade layout. Dusty Robotics FieldPrinter has revolutionized how construction teams conduct layout and manage operations in the field. Instead of individual trades manually measuring and marking layout based on the coordinated model, the FieldPrinter prints the virtual design and construction (VDC) model directly on the construction site surface with 100% accuracy. Layout across all trades can be printed concurrently, significantly compressing construction schedules and improving cross-trade collaboration.
Skanska, one of the largest construction and development companies in the world, used the Dusty Robotics FieldPrinter to build a healthcare facility three months ahead of schedule and $3 million under budget.
Safety KPIs
Central to any construction project is the safety of its workers. Safety KPIs allow organizations to determine their safety programs' effectiveness and ensure everyone involved adheres to critical protocols.
Construction is inherently hazardous, with workers often exposed to risks around heavy machinery and complex work processes. By tracking safety KPIs, businesses can keep workers compliant with regulatory standards. They can also identify areas for improvement and, in doing so, avoid legal repercussions and maintain a well-polished industry image. Safety KPIs can also lead to significant financial benefits, as fewer incidents mean fewer injury-related costs and reductions in insurance premiums.
While there are a plethora of helpful safety KPIs to track in construction, some of which may be unique to each organization, the most common ones include:
- Worksite accident rate
- Total recordable incident rate (TRIR)
- Lost time injury frequency rate (LTIFR)
- Near miss reporting rate
- Safety training compliance
- Safety audit score
A safer work environment helps boost company morale and productivity. Safety KPIs drive proactive intervention so that businesses can continually work to foster a culture of safety. Part of that responsibility includes limiting the type of work that is known to cause injuries, even in the long term. For instance, manual layout requires foremen from each trade to bend over thousands of times daily to manually measure and mark the floor. This is known to cause repetitive motion injuries, such as chronic lower back pain, which reduces the quality of life for individuals.
Quality KPIs
In construction, quality KPIs help stakeholders evaluate project quality standards. Without solid quality control measures in place, businesses may experience safety issues, structural defects, and budget and schedule overruns. Overlooking quality control can lead to serious financial repercussions. If quality issues get overlooked during layout, they can result in the need for rework after installation, which is both expensive and time-consuming.
Ensuring high-quality outcomes is also vital to improving the customer experience and maintaining a company's reputation. If quality expectations are unmet, clients may become dissatisfied, significantly impacting the builder’s reputation and future opportunities.
The following quality KPIs should be measured as part of any robust project strategy:
- Defect density
- Customer satisfaction score (CSAT)
- First-time quality (FTQ)
- Rework percentage
- Materials inspection pass rate / material defect
The good news is that carefully monitoring quality KPIs can help to avoid these issues. Doing so establishes a culture of perpetual improvement where lessons from one project can be applied to future endeavors, keeping quality at the forefront of all processes. In addition to tracking quality KPIs, construction teams must embrace innovative construction technology that automates error-prone processes and improves the quality of work in the field.
Quality-driven GCs use multi-trade layout to remove the risk of quality errors in layout. The Dusty Robotics FieldPrinter prints multi-trade layout with 100% accuracy while also empowering teams to print additional information such as text, room labels, QR codes, and more to guide installation. As Jim Hull, Senior Project Manager at Turner Construction explains, “The FieldPrinter has increased layout speed by 5X and provides 100% accuracy, eliminating the need for re-work on Turner projects.”
How Dusty Robotics Can Improve Your Construction KPIs
With so many different types of KPIs to keep track of, it’s essential to use innovative tools that keep your team on schedule, under budget, and up to quality standards. Dusty Robotics FieldPrinter sets the standard for excellence, leadership, and innovation. The top GCs in the industry use the FieldPrinter to guarantee layout accuracy, compress construction schedules, eliminate the need for rework, and maximize profitability.
Dusty Robotics provides flexible pricing options that enable builders to harness the power of the FieldPrinter across various projects, timelines, and budgets.