How to Improve Collaboration in Construction
.jpg)
Collaboration drives successful construction projects. It’s the collective effort of diverse professionals, each bringing unique expertise to the table, that turns designs into tangible reality. In large-scale and complex projects, seamless collaboration ensures that all moving parts align efficiently, within budget, and on schedule.
This mutual interdependence extends beyond technical tasks. It fosters a culture of shared responsibility and accountability. Without effective collaboration, projects often face costly delays and quality issues. Even more concerning, a lack of synergy compromises the safety and longevity of structures.
Collaboration isn’t just a desirable trait in the construction industry—it's necessary for the success and safety of all involved. It binds teams together with trust, streamlines processes with clarity, and ensures the efficient construction of quality structures that stand the test of time.
What is Collaboration in Construction?
Collaboration in construction involves open communication, shared responsibility, and the alignment of visions. Good collaboration acts as a well-oiled machine. Architects and designers lay the foundational vision, ensuring that the project's aesthetic and functional elements integrate seamlessly.
The various trades contribute their expertise while actively communicating with one another to promote seamless workflows and reduce inefficiencies. Subcontractors, often handling specialized parts of a project, need a clear line of communication with general contractors and other stakeholders. This keeps everyone on the same page.
Technology plays a pivotal role in fortifying this collaboration. Virtual Design and Construction (VDC) software, especially Building Information Modeling (BIM) software, has revolutionized the industry. BIM allows all stakeholders to visualize the project in 3D, identifying potential issues or clashes before physical construction even begins. This preemptive identification saves time and money.
Now, envision taking this digital collaboration directly into the field. Automated multi-trade layout does just that. It bridges the gap between digital design and physical reality by directly printing the coordinated digital model onto the construction site surface. This groundbreaking approach results in unparalleled accuracy and on-the-ground collaboration.
Traditional Challenges of Collaboration in Construction
The lack of a multifaceted, well-organized process for collaboration can lead to serious consequences ranging from project delays and rework – to lost revenue. Here are the most common challenges that prevent effective collaboration on construction projects.
Communication Gaps
Effective communication is the cornerstone of a successful construction project. However, two distinct sets of communication gaps can significantly impact project outcomes: the first pertains to the challenges between design and architect teams, and the second revolves around the communication disconnect between the design, layout, and installation stages.
Communication Gaps Between Design and Architect Teams
Architects play a pivotal role in crafting the overarching vision for any construction project, translating abstract ideas into tangible concepts. Subsequently, design teams ensure that this vision is aesthetically pleasing, technically feasible, and functional. Nevertheless, these two crucial groups often encounter communication gaps stemming from misinterpretations, ambiguous instructions, or a lack of clarity regarding the design's intent.
Such a lack of communication can lead to project outcomes that are misaligned with the initial vision, resulting in costly rework and delays. The structures constructed based on miscommunicated designs may fail to meet the desired aesthetic or functional standards, causing dissatisfaction among both the project's workforce and stakeholders. Inadequate communication can have significant financial repercussions, with businesses incurring rework costs of as much as $31 billion annually.
Communication Challenges During Layout and Installation
Construction projects' layout and installation phases demand close collaboration among all trades, including mechanical, electrical, plumbing, drywall, and others. Each trade has its unique set of specifications and requirements. Without clear guidelines or overlapping instructions, these trades often work at cross-purposes, leading to installation issues and on-site conflicts.
Mistakes made during the layout and installation phase can have far-reaching consequences, potentially resulting in significant structural problems in the later stages of the project. For instance, improperly placed electrical conduits might clash with plumbing lines, necessitating time-consuming and costly rectifications. Such mishaps disrupt the project schedule and increase overall project durations.
To mitigate these communication gaps and ensure the successful execution of construction projects, it is essential to establish open lines of communication throughout all project phases and use construction technology to mitigate these issues. Using technology like the Dusty Robotics FieldPrinter means that your project will benefit from automated multi-trade layout instead of challenging communication issues. This technology accurately brings the architects' and designers' communication and collaboration into the field for all trades during the layout stage. Automated multi-trade layout streamlines the installation phase, enabling it to commence sooner and proceed smoothly. By addressing these communication challenges, construction teams can enhance project efficiency, minimize rework, and deliver results that align with the initial vision.
Fragmented Workflows
The construction process is a symphony of coordinated actions. Fragmented workflows, where tasks are isolated rather than being part of an interconnected process, lead to inefficiencies across the board. Such fragmentation might arise due to a lack of standardized procedures, poor project management, or the absence of a unified vision.
Fragmented workflows often result in duplicated efforts or tasks done out of sequence. This disjointed approach prolongs project timelines and compromises the quality of the finished structure. To understand this, think about how manual layout is isolated across trades. It prevents visibility into the holistic instructions for installation– even if the layout for plumbing makes perfect sense to the plumbers, it may interfere with plans created by the electricians.
Information Silos Between Trades
In many projects, each trade has its own set of information, tools, and processes. When these trades operate in isolation, information silos emerge. These silos prevent teams from comprehensively viewing the project, thereby hindering holistic decision-making.
It’s hard to make informed decisions when working in a silo, and manual layout's sequential nature only complicates things. Mechanical, electrical, plumbing, and drywall manual layout is conducted individually, one after the other on the schedule. This creates major pain points when scheduling and creates the opportunity for layout errors and discrepancies that require remediation. It’s not that the trades work in conflicting ways on purpose; rather, the silos created by sequential layout are simply unavoidable. These silos can create structural inconsistencies, wasted materials, and a rise in operational costs. Moreover, the lack of shared knowledge will likely prevent the project from reaching its full potential.
Limited Technology
While modern construction technology offers tools to streamline operations and improve collaboration, many firms are slow to adopt these advancements. This reluctance is often due to budgetary constraints, resistance to change, or a lack of awareness about available solutions.
Relying on outdated methods or limited technology can significantly hinder a project's efficiency. Without modern construction technology, potential design conflicts go unnoticed until they cause real-world issues.
New technology makes work faster, safer, and more profitable for construction firms. Without these tools, your firm’s construction capabilities will fall behind your competitors, and your customers will become frustrated with your slower turnaround times and the amount of rework that needs to be completed. But when you adopt technological advances like VDC software and robotic multi-trade layout, you bring your firm into the modern age. You reduce the amount of additional incurred expenses and rework and improve your first-time outcomes. Your build sites are safer, and your construction is faster. These advantages will keep your customers happy and significantly improve your bottom line.
Constraints and Changes in Scope
Construction projects operate within predetermined time and budget constraints. Unforeseen challenges or evolving client demands can lead to changes in scope, placing additional pressure on these already tight parameters. Manual project planning and forecasting only compounds these issues and can lead to serious delays affecting the entire project.
Without corresponding adjustments in time or budget, alterations in scope can strain resources and manpower. Teams are forced to rush tasks, compromising work quality. Budget overruns sour client-contractor relationships, and rushed timelines lead to mistakes and safety oversights.
Benefits of Successful Construction Collaboration
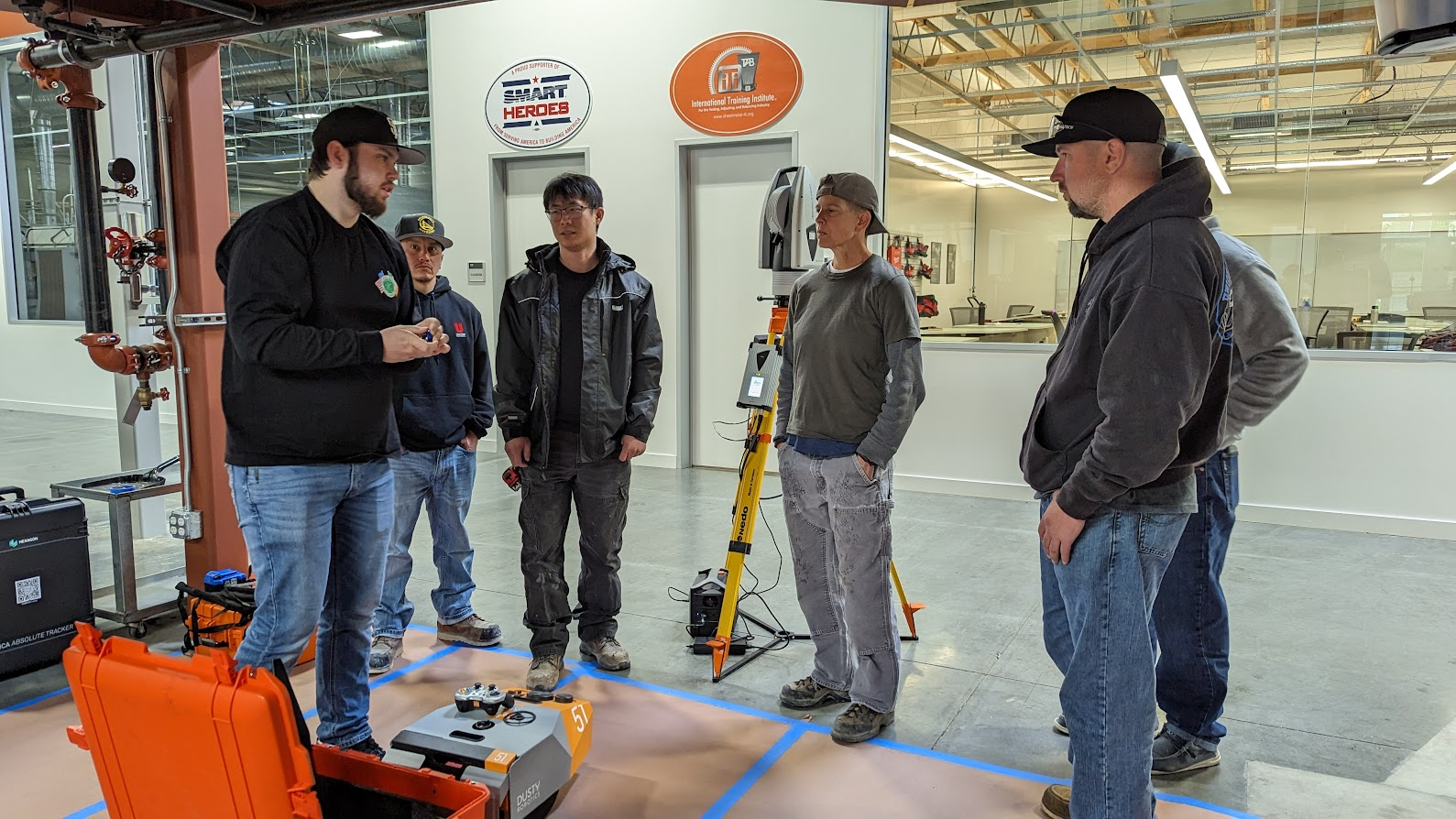
Considering the host of problems that can arise from poor collaboration, businesses have every reason in the world to promote better communication between teams. The benefits of successful collaboration are extensive and reach far beyond the duration of the project itself.
Cost savings are one of the greatest benefits of good collaboration. Shared resources, reduced rework, and efficient use of time all contribute to significant cost savings for the entire project. Additionally, collaboration improves teams’ skills and expertise. When designers, architects, and tradespeople work together, they can spot potential issues early, ensuring the final product meets the highest quality standards. This leads to better project efficiency, as effective collaboration streamlines operations and reduces redundancies. When teams communicate clearly and share resources widely, they move quickly from one phase to the next. A coordinated approach ensures that everyone knows their role and timeline, leading to smoother transitions and minimized downtime.
To understand how effective collaboration can improve your construction project, you only have to look at how Skanska leveraged the Dusty Robotics FieldPrinter. Using automated multi-trade layout, Skanska completed a best-in-class healthcare facility 3 months ahead of schedule and $3 million under budget.
Client Satisfaction and Competitive Advantages
Collaborative teams benefit from a more holistic project view, which helps identify and mitigate potential risks. By pooling their experiences and insights, teams can foresee challenges and devise strategies to navigate or mitigate them. This improves team morale and trust, and returns dividends beyond the immediate team satisfaction. Your clients will appreciate your coordination efforts, too. Successful collaboration often results in projects delivered on time, within budget, and to the expected quality. Satisfied clients that are more likely to return for future projects and recommend the business to others.
Tips For Improving Collaboration on Construction Projects
Effective collaboration on construction projects demands clear communication and advanced planning. Leveraging digital tools, fostering a culture of open feedback, and ensuring aligned objectives fosters better teamwork. Prioritizing these strategies ensures timely project completion and optimal resource utilization.
Start Collaboration Early
Starting collaboration early, especially during the design phase, is paramount. Using VDC software like BIM allows teams to visualize, analyze, and resolve potential issues before they arise on-site. Integrating this with robotic layout translates the digital plan into physical reality, ensuring that the on-field work aligns with the collaborative designs.
Include Important Stakeholders Right Away
Including stakeholders from all trades early in the project ensures holistic planning and foresight. Engaging owners continuously maintain transparency about scope changes. By aligning budgets, schedules, and other critical aspects from the onset, organizations can mitigate misunderstandings and foster a unified approach to achieving project objectives.
Have Strong Leadership
Strong leadership is vital for project success. Identifying leaders, such as project managers, superintendents, and design teams, is key. Strong leaders are willing to adopt modern strategies and tools that facilitate collaboration and efficiency and drive their company’s competitive edge. These leaders know the value of maintaining relevancy and choose to embrace technology that ensures streamlined operations and comprehensive project completion.
Build Trust and Open Communication
Trust is the cornerstone of successful construction projects. It requires open communication, where feedback is encouraged, and accountability is emphasized. With trust, team members collaborate effectively and make sure the project's objectives are met with shared dedication and mutual respect. Trusting your layout is important, too; when your layout is accurate and aligned across trades, your labor force feels more secure in their ability to complete work the first time. They won’t feel frustrated or annoyed that the company wastes their time with the inefficiency of sequential manual layout or avoidable errors.
Utilize Multi-Trade Layout Technology
Multi-trade layout increases operational efficiency and compresses construction schedules to deliver results at a fraction of the time required by manual layout. Instead of scheduling each trade’s layout individually, automated multi-trade layout prints all trades’ layout concurrently with 100% accuracy. This guarantees that systems like plumbing, electrical, HVAC, and structural components coexist without interference.
Effective multi-trade layout prevents on-site clashes and saves time. By printing the coordinated digital model directly on the construction site surface, foremen from each trade can walk the floor together and collaborate effectively. They are empowered to quickly evaluate the detailed layout and can identify and resolve potential problems before any construction begins. This precludes the need for rework, prevents delays, and makes all parties happy.
For those who have worked on siloed trade teams and inefficient construction projects, multi-trade layout may seem too good to be true. But robotic layout has already helped dozens of construction teams achieve real results. Discover how Turner, an international construction services company, used Dusty Robotics FieldPrinter to increase layout speed by 5X, provide 100% layout accuracy, and eliminate the need for re-work.
Contact us today to learn how the FieldPrinter can improve collaboration and compress schedules for your next construction project.